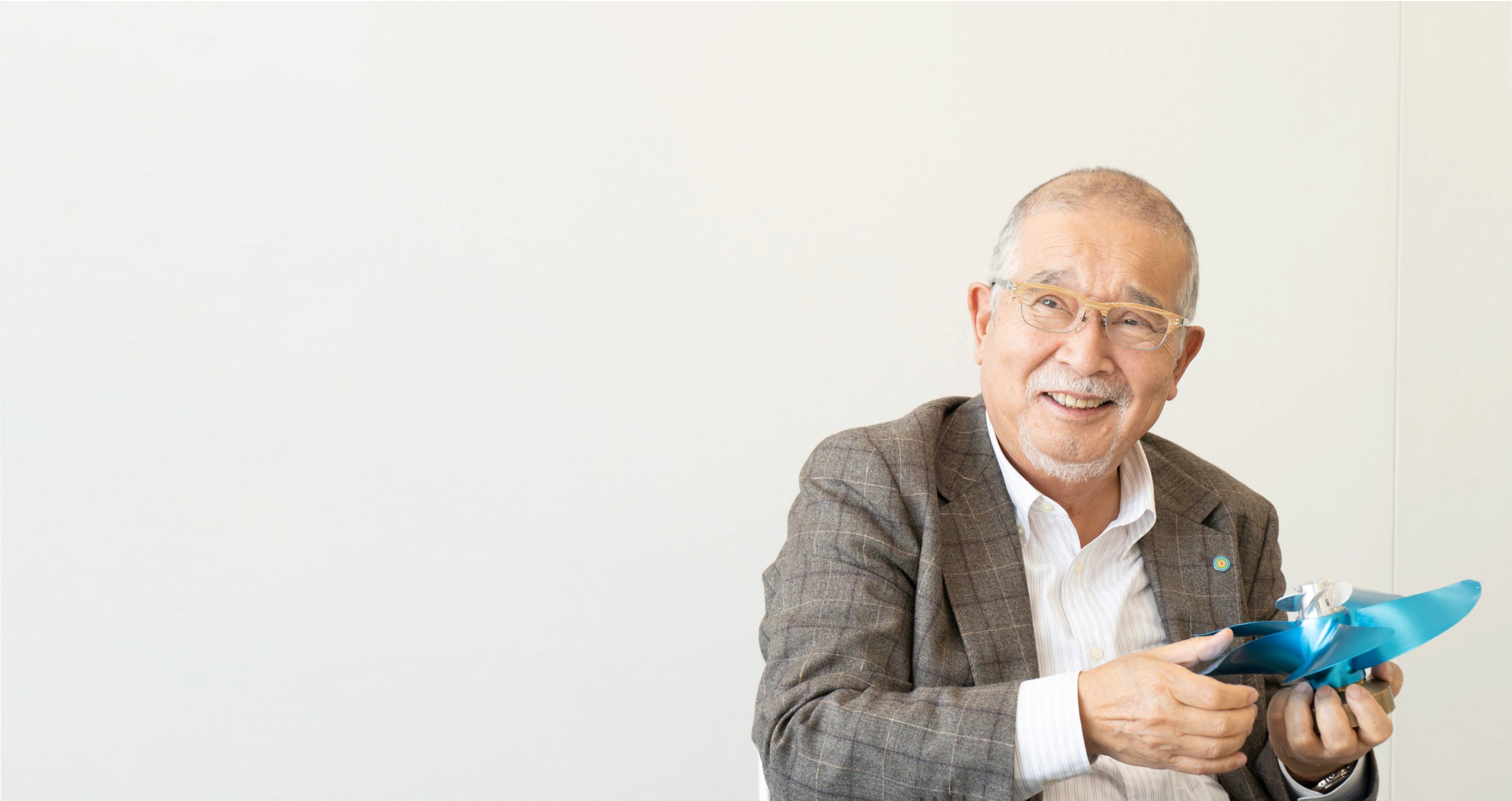
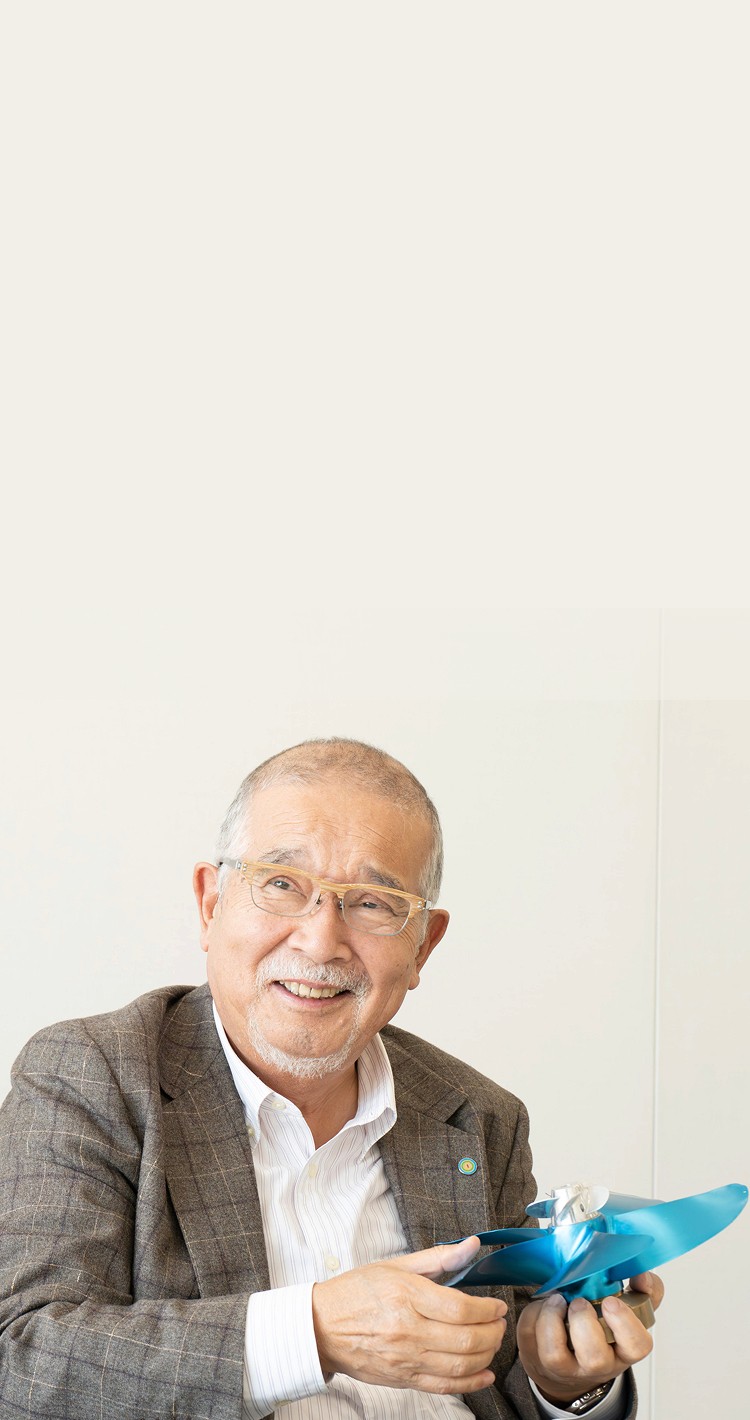
Curiosity is the spark of everything.
The relentless pursuit of success
in PBCF development.
PBCF Initial Developer
Kazuyuki Ouchi
The Propeller Boss Cap Fins (PBCF), an energy-saving device for ships developed and sold by MOL Techno-Trade, Ltd., has significantly contributed to reducing the environmental impact by improving the fuel efficiency of ships worldwide. We interviewed Dr. Ouchi, the developer of PBCF, about the motivation for its development, the journey to commercialization, his activities after PBCF development, and his future outlook.
Encountering the Maritime Industry
- Could you tell us what led you to become involved in the maritime industry?
-
Since childhood, I've loved creating things, and I vaguely aspired to do "big work" and "creative work." When I took the university entrance exam, I failed to get into my first-choice architecture department and ended up in the naval architecture department. Actually, I became so absorbed in jazz at university that I neglected my studies and spent all my time in the jazz club (laughs). I had studied hard in high school, but once I got into university, I lost my sense of purpose, like a kite with a broken string.
At that time, student movements were very active, including the Yasuda Auditorium incident. I sometimes participated in demonstrations, but I couldn't keep up with their radical activities like wearing helmets and carrying wooden sticks.
As a result, I wasn't motivated in my job hunting, and I ended up graduating late. - Why did you choose the field of shipbuilding?
-
When I was a sophomore in college, it was time to think about my future career. Among various options, I ultimately chose the path of naval architect because "I liked large structures and dynamic things."
Initially, I aimed for the architecture department, but I gave up because my grades weren't good enough. I was also interested in the aviation industry, but at that time, aircraft development was restricted by the GHQ in Japan. I also considered shipbuilding companies as an option, but I wanted to manage and build entire ships, and in a shipyard, each person is only responsible for designing a part of the ship.
After considering various options, I was attracted to the world of shipping companies where I could freely design and them various ships.
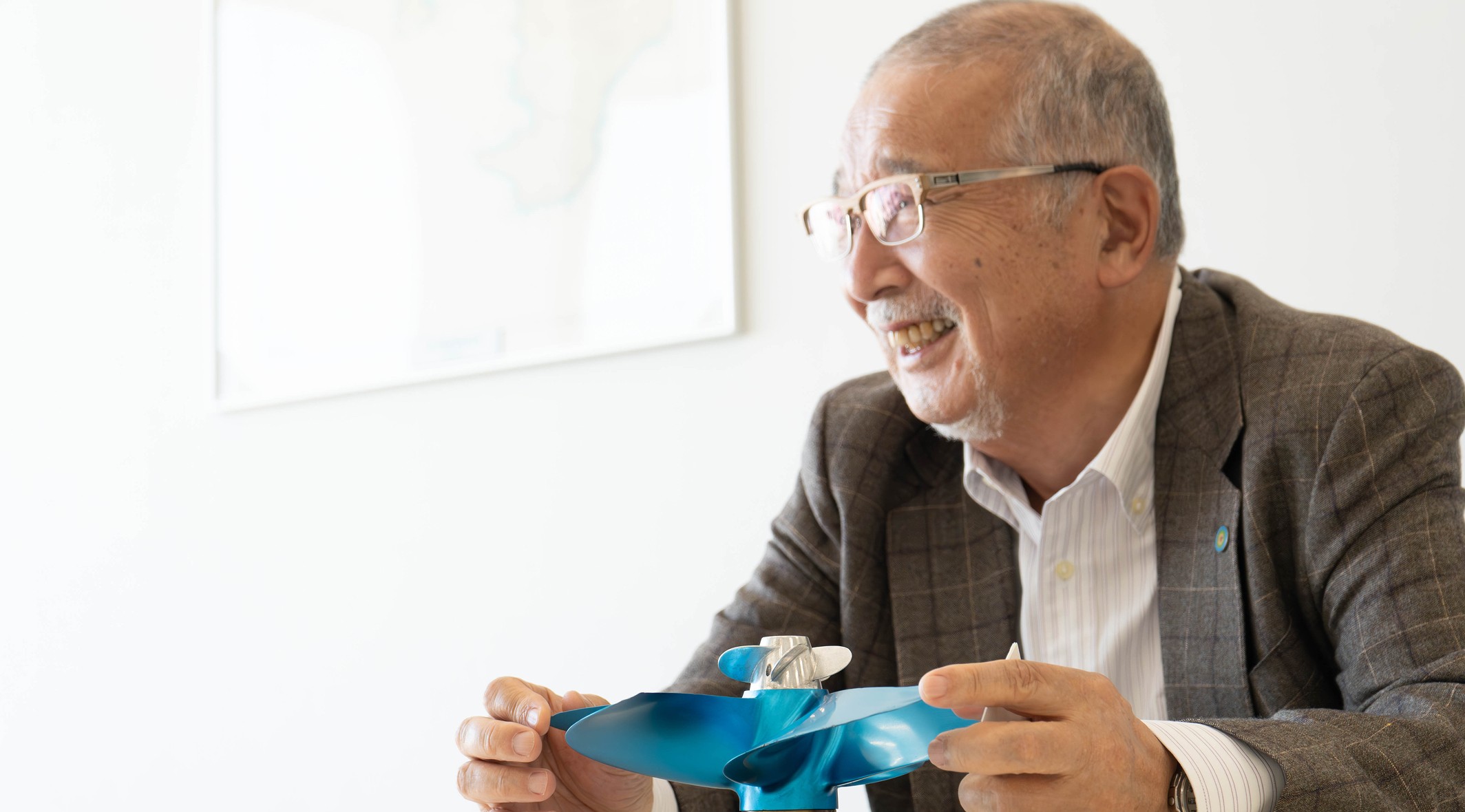
Work at Mitsui O.S.K. Lines
- What kind of work did you do after joining Mitsui O.S.K. Lines?
-
After joining Mitsui O.S.K. Lines, I worked at a shipyard in Tamano, Okayama Prefecture, supervising the construction and repair of ships. Later, I became involved in an LNG carrier newbuilding project. It was a very rewarding job, obtaining overseas licenses and building the first LNG carrier in Japan. However, I became ill and was told by the doctor to stop.
I had damaged my liver. It was just before I was about to become a section manager, but I had to leave the project. - What were your thoughts at that time?
- From the beginning, I was disappointed with the company. There was a lack of technology. The main job was maintaining and managing ships, and they were not very active in developing new technologies. I did the job thinking it was also a job, but I wanted to do more creative work.
The Inspiration Behind PBCF Development
- Was that the catalyst for developing PBCF?
- Yes, I was later transferred to the technical department, where I started developing PBCF. The trigger was meeting Mr. Ogura, the president of West Japan Flued Engineering Laboratory . He was a propeller expert and was exploring new propeller ideas at the time. As we discussed various ideas, the concept of PBCF was born.
- What was the initial idea?
-
Mr. Ogura thought that propulsion efficiency would improve by placing propellers of the same diameter before and after the propeller. However, the experimental results were not favorable. So, I suggested, "What if we make the diameter of the rear propeller smaller?" Then, we saw signs of improved propulsion efficiency.
We thought this was interesting and started working on development in earnest.
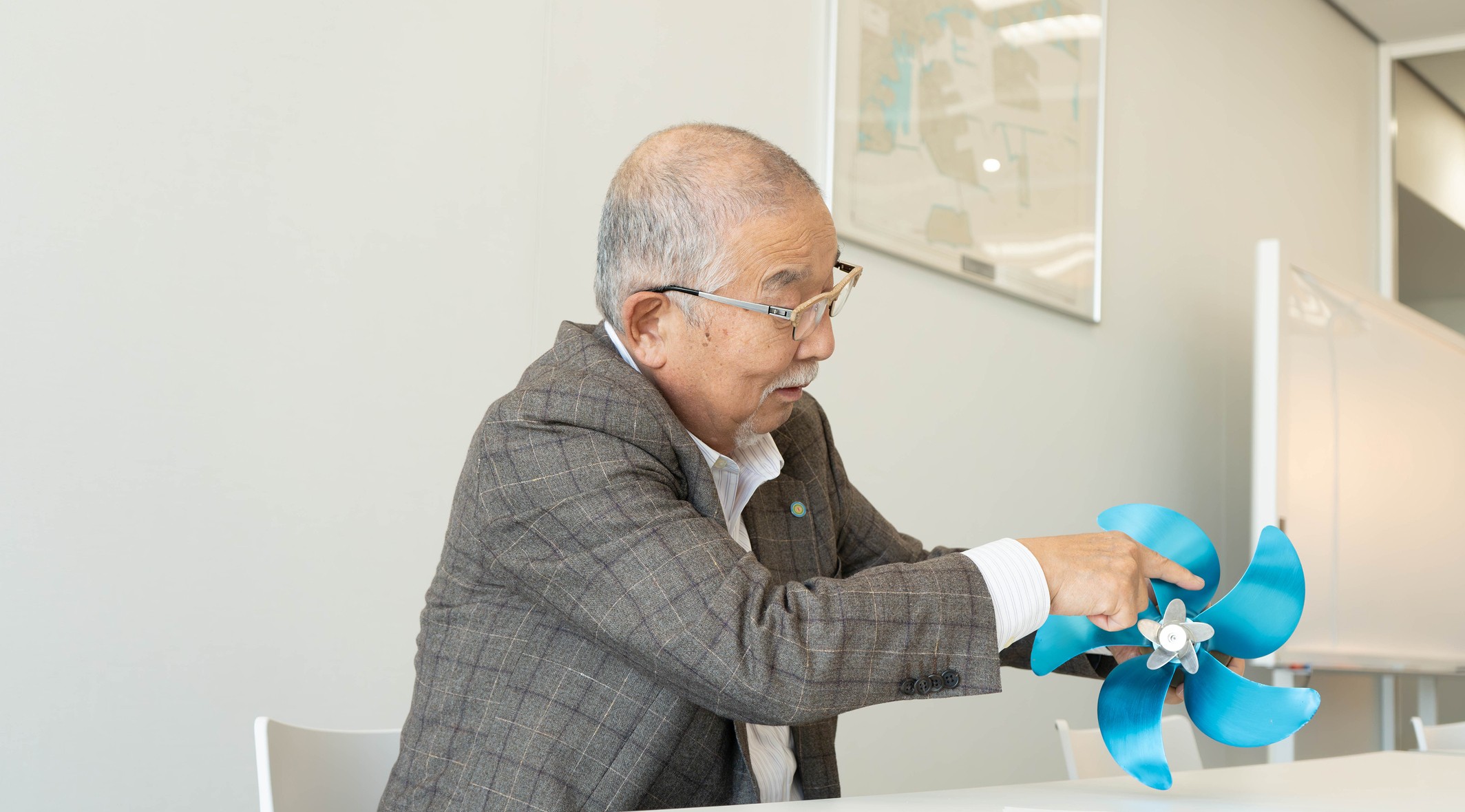
The Journey to Commercialization - A Series of Trial and Error
- What difficulties did you encounter before commercialization?
- The development of PBCF was not a smooth road. Several problems occurred, the blades of the PBCF cracked, and the desired effect was not achieved, etc. We faced technical challenges as well as opposition from inside and outside the company.
- What kind of challenges did you face?
- First, it was necessary to create various prototypes and repeat water tank experiments to determine the shape of the PBCF. We conducted water tank experiments until late at night, sometimes working through the night. Also, ensuring the strength of the PBCF was a major challenge. The initial prototypes lacked strength, and when they were installed on actual ships, the blades broke. We had to identify the cause and revise the materials and design to improve strength.
- What was the reaction from those around you?
- When the lack of strength was discovered after selling PBCF for 20 ships, everyone in the it," and "Should we just stop?"
- Why did you continue development without giving up?
- Because I had a strong belief that "PBCF will definitely succeed." Also, the ability to involve many people around me was significant. Many companies, such as West Japan Flued Engineering Laboratory and Mikado Propeller, cooperated in the development of PBCF. We could not have completed PBCF without their cooperation.
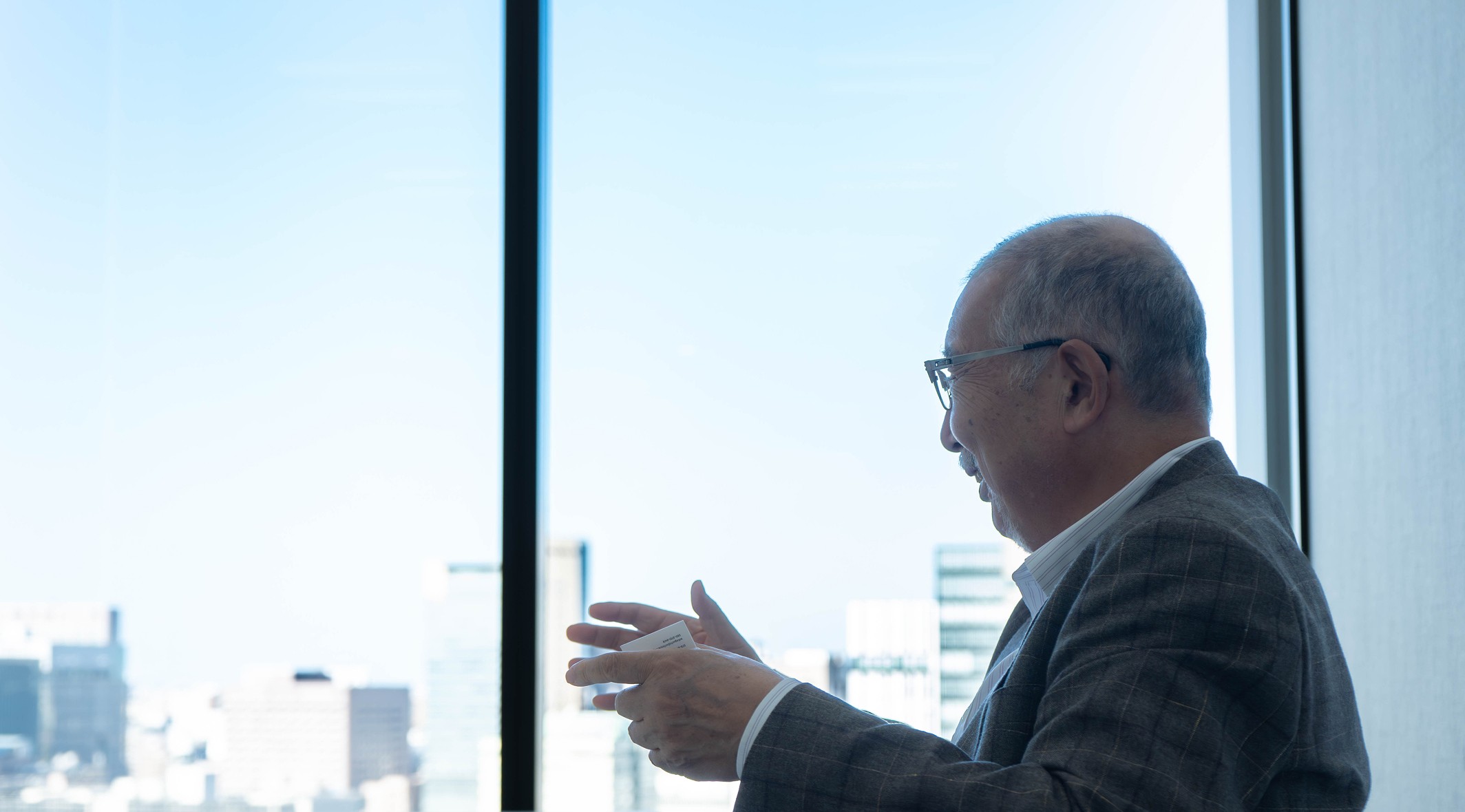
Adoption by a Rival Company - Nippon Yusen
- How did you view the presence of your rival company, Nippon Yusen (NYK)?
-
When selling PBCF, the presence of Nippon Yusen could not be ignored. Nippon Yusen was initially reluctant to adopt PBCF. So, I asked a classmate from my university days, who was then a Managing Director at Nippon Yusen, for cooperation.
As a result, Nippon Yusen also adopted PBCF, which accelerated its spread. The fact that a rival company adopted PBCF made other shipping companies interested in PBCF.
Independence from a Major Company - A New Challenge
- You were still in Mitsui O.S.K. Lines after developing PBCF, but why did you decide to become independent?
- Through the development of PBCF, I realized the difficulty of creating new technologies within a company. In large corporations, you are inevitably bound by the logic of existing businesses and organizations, which hinders free thinking and challenges. I wanted to shape my ideas more freely. That's why I left Mitsui O.S.K. Lines and established my own consulting company.
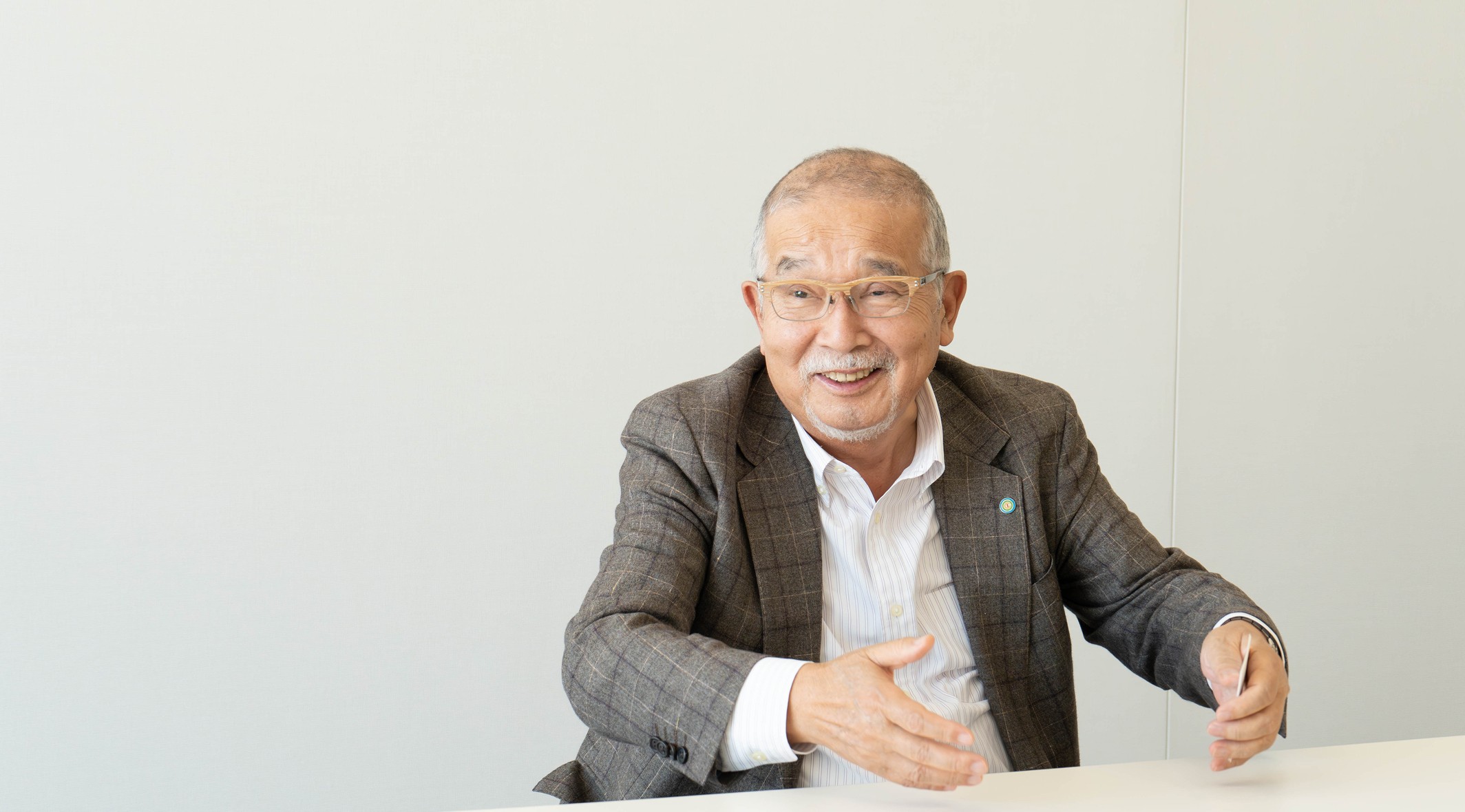
Challenging the Wind Challenger - Pursuing a Dream
- What prompted you to start developing the Wind Challenger?
- Energy saving is the most important issue for us, and it also leads to preventing global warming. Wind power, a zero-emission propulsion, does not use fossil fuels. Wind power propulsion is an old technology, but it has been attracting attention again in recent years due to growing concerns about environmental issues. So, I started developing a ship called "Wind Challenger," equipped with a wind power propulsion system.
- Was the development of the Wind Challenger smooth?
- Of course, it was not easy. There were many challenges to overcome, such as designing the wind power propulsion system and balancing it with the ship’s hull. However, the experience gained from developing PBCF and the ability to involve people around me were significant weapons in the development of the Wind Challenger.
- And finally, the first Wind Challenger ship, "Shofu Maru," was completed.
- Yes, " Shofu Maru" has received high praise from both domestic and international sources, including winning the Ship of the Year 2022 award. The wind power propulsion system is a revolutionary technology that can contribute not only to reducing the environmental impact but also to reducing fuel costs. It is attracting attention from the shipping industry around the world.
- You were awarded the Prime Minister's Award for these achievements.
- I am very honored. The development of PBCF and the Wind Challenger could not have been achieved by my efforts alone. We have come this far thanks to the cooperation of many people.
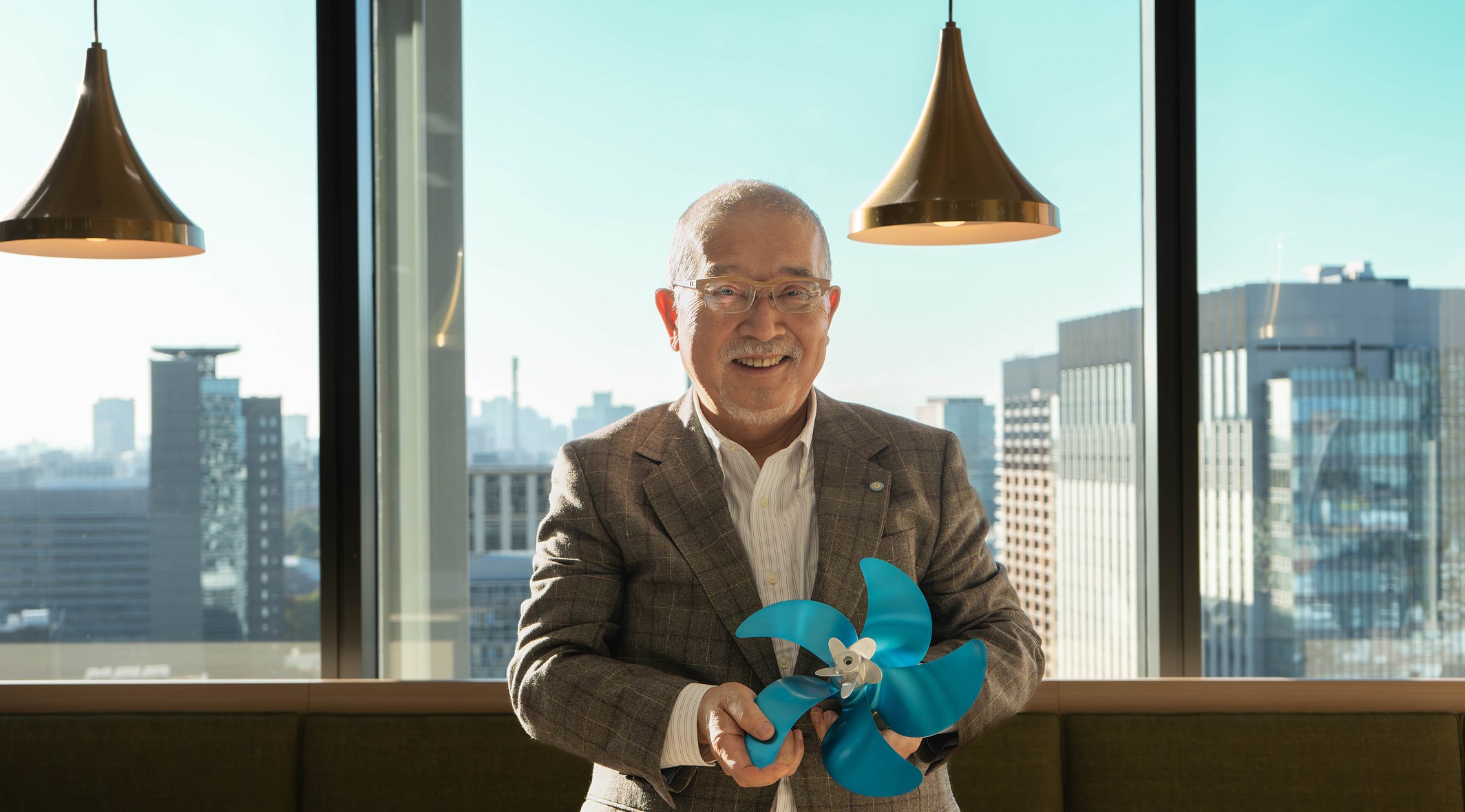
The Future of PBCF - To the World's Oceans
- Please tell us about the future outlook for PBCF.
- Currently, there are more than 40,000 ships operating worldwide, but only about 4,000 of them are equipped with PBCF. I believe there is still room for further adoption. PBCF is a device that can contribute not only to energy saving but also to reducing CO2 emissions. As environmental issues become more serious, the role of PBCF will become increasingly important.